If you are getting surface finishes like the ones shown below then perhaps you need to consider some maintenance on your live tool holders.
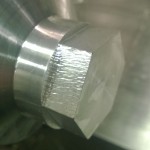
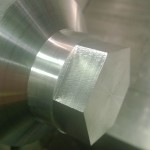
Regular inspection and maintenance of live tool heads can increase service life by as much as five times. A live tool system preventive maintenance program ensures part accuracy, increases cutting tool life, reduces scrap, improves reliability and overall confidence in lights-out operations, and lowers overall toolholder costs.The following five-point inspection can help ensure live tool heads deliver high value and production accuracy.
1. Measure spindle runout. Rest a dial test indicator tip on the inner surface of the collet pocket and rotate the live tool head. The maximum runout for live tools is typically around five microns in the collet pocket. If in excess, then the problem could be a bent spindle or bad bearings. Excessive runout in the spindle puts an additional load on the bearings, ultimately decreasing overall service life.
2. Check for radial play. While the dial test indicator is in the collet pocket, simultaneously check for radial play. If movement shows up on the indicator when toggling the spindle, then there is a problem with the bearing preload; the bearings and seals should be replaced.
3. Examine the rotation. Live tool heads should rotate smoothly, be free of any binding, and should have no real audible noise coming from the bearings while spinning the tool. This can be rated on a scale of 1-5.
4. Visually inspect the live tool head. Check for any damage from crashes, excessive wear to the drive coupling, or rust in the collet pocket.
5. Inspect for coolant contamination. Coolant contamination is the number one failure mode of live tool holders, and the catalyst is heat buildup. If live tool heads get too hot, the heat can deform, swell, or burn the contact surface of the seals that hug the spindles, making it easy for the coolant and fine metal chips to enter the heads and begin the degradation process. If the live tool holder has an easily accessible cover plate, remove it and inspect for coolant contamination. Proper coolant care is the only controllable variable in increasing live tool head service life, it’s also important to maintain coolant concentration by measuring it using a refractor as opposed to visually with the naked eye. A refractor can determine if the coolant is rich or lean. If the concentration is rich and more concentrate is added, there becomes a reduction in coolant capacity. On the other hand, if the coolant is lean and not enough concentrate is added, there becomes the risk of shorter tool life, poor surface finish and machine corrosion.
While exact maintenance intervals and service life for a live tool head depend on application variables such as workpiece material type, cycle times and coolant condition, a general rule is to perform the five-point inspection at least every three months. Maintain a log of inspection findings to track a live tool head’s performance throughout the years. This will help indicate when it is time to remove a live tool head for routine maintenance and help establish an accurate maintenance budget. Be sure to record findings specific to the coolant maintenance to track when the system requires cleaning or a new coolant batch. Include details such as concentration ratio, filtration system, water hardness and bacteria levels.